The maritime industry heavily relies on the availability of spare parts to ensure that ships operate smoothly without any unnecessary downtime, especially for marine purifiers, which consist one of the most crucial parts of machinery aboard any vessel.
Equivalent spare parts of OEM specifications for marine purifiers have been an excellent option for ship owners who wish to combine cost-effectiveness, reliability, and performance. On the other hand, it is imperative for ship operators and maintenance crews to have a comprehensive understanding of the engineering behind alternative spare parts for marine purifiers and thus make informed decisions.
The Process of Designing Alternative Spare Parts for Marine Separators
Manufacturers who produce alternative spare parts for marine purifiers use a range of strategies to ensure their products match or even surpass OEM (Original Equipment Manufacturer) specifications. These strategies include:
1. Detailed Analysis of OEM Parts
Manufacturers carefully analyze the design, materials, and specifications of OEM parts to understand how they function and their performance requirements. This analysis serves as a blueprint for creating equivalent parts for marine purifiers that replicate the original components’ essential features and dimensions.
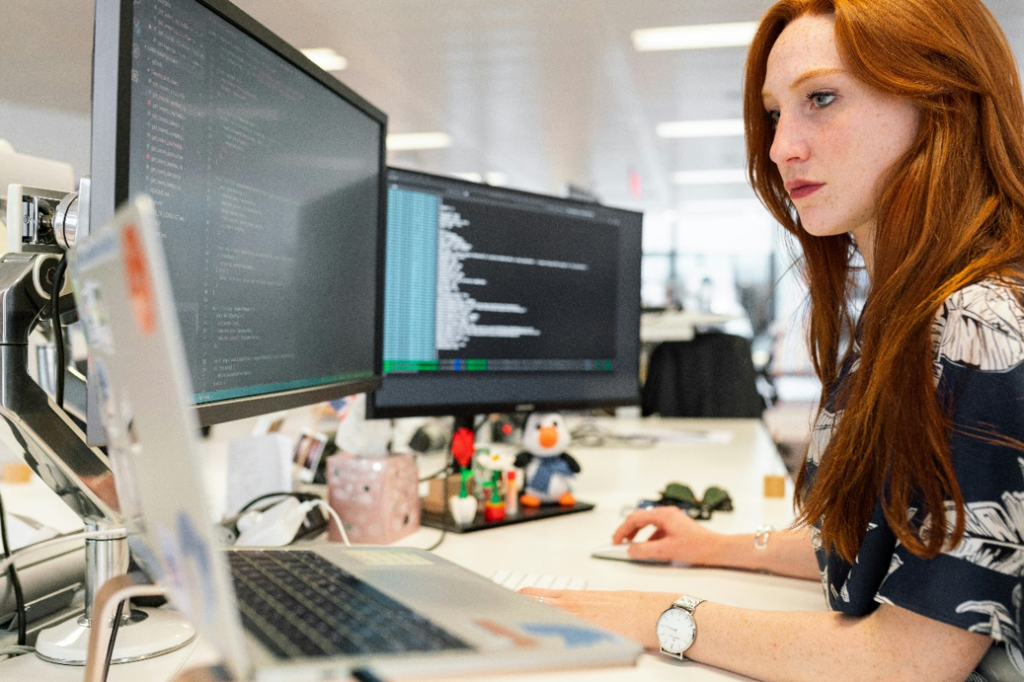
2. Reverse Engineering
Reverse engineering involves disassembling and analyzing OEM parts to understand their internal structure, dimensions, material & necessary tolerances that are crucial for exact reassembling and high performances. Manufacturers use advanced imaging technologies, such as 3D scanning and computer-aided design (CAD), to create accurate digital models of the parts. These models serve as a basis for designing alternative parts that match the OEM specifications of marine purifiers.
3. Material Selection
Manufacturers choose materials that meet or exceed the properties of those used in OEM parts. They consider factors such as corrosion resistance, mechanical strength, and temperature tolerance to ensure that the alternative parts perform reliably in marine environments. Material testing and analysis help verify that the selected materials meet the required specifications.
4. Precision Manufacturing
Precision manufacturing techniques, such as CNC machining and additive manufacturing (3D printing), are used to produce marine purifier alternative parts with tight tolerances and accurate dimensions. Advanced machinery and quality control processes ensure each part conforms to the specified dimensions and features outlined in the OEM specifications. ZEDMAR has been incorporated utilizing state of the art machine tools attaining tolerances up to +/-0.0019 mm.
5. Quality Assurance Testing
Manufacturers conduct thorough quality assurance testing to confirm the performance and durability of alternative parts. Testing may include functional tests, pressure tests, and endurance tests conducted under simulated operating conditions to ensure that the parts meet OEM standards for reliability and performance in marine purifiers.
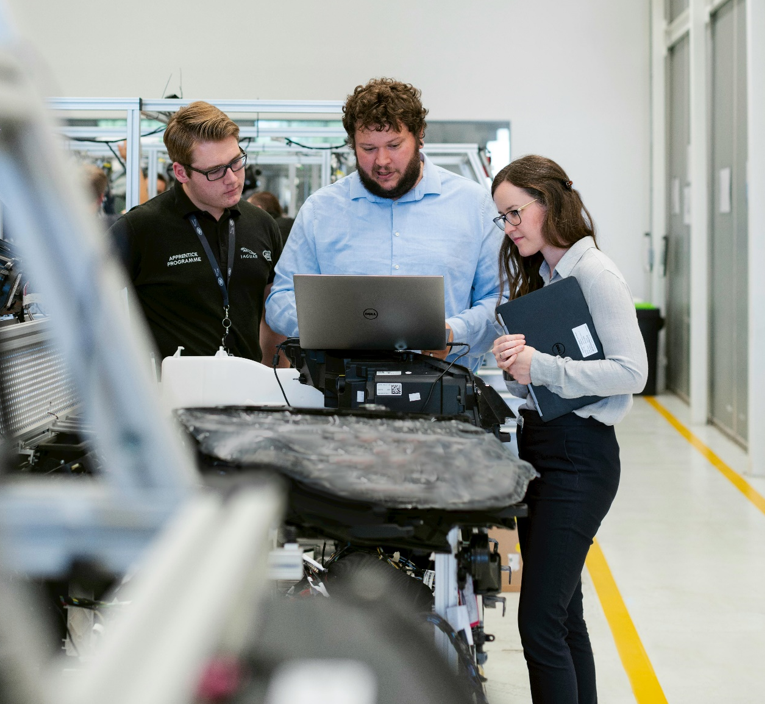
6. Feedback and Continuous Improvement
Manufacturers gather feedback from customers and end-users to identify areas for improvement and ensure their alternative parts effectively meet the market’s needs. Continuous refinement of manufacturing processes and material selection helps manufacturers maintain consistency and quality in their products over time.
By implementing these strategies, manufacturers of equivalent spare parts for marine purifiers can confidently assure customers that their products meet or exceed OEM specifications. This provides ship operators and maintenance crews with reliable and cost-effective alternatives.